Вертикально-сверлильные станки (ВСС) предназначены для сверления, рассверливания, зенкерования, зенкования, развертывания и растачивания отверстий со сравнительно невысокими требованиями к точности; нарезания резьбы, а также фрезерования (как правило, с ограниченными режимами.) плоскостей и пазов.
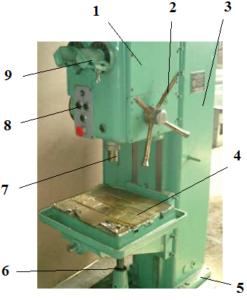
Рис. 4.28. Вертикально – сверлильный станок: 1 – коробка скоростей; 2 – штурвал вертикального перемещения шпинделя; 3 – колонна; 4 – стол; 5 – основание; 7 — шпиндель; 8 – пульт управления; 9 – механизм настройки частоты вращения шпинделя
В качестве основного параметра станков принимается наибольший, условный диаметр сверления в деталях из стали средней твердости (сталь 45 по ГОСТ 1050-88). Если предусматривается возможность фрезерования, то станки обязательно оснащаются координатными столами с ручной или механической подачей, а шпиндель станка сконструирован с учетом восприятия радиальных нагрузок. Размеры ВСС с условным диаметром сверления 1-80 мм стандартизованы (ГОСТ 170-93).
По своему назначению ВСС имеют несколько исполнений. Однако общим признаком этих исполнений является то, что шпинделя станков конструктивно выполнены в варианте выдвижного, т.е. движение подачи шпинделя при резании осуществляется за счет вертикального перемещения пиноли, расположенного в скоростной коробке станка. На рис. 4.28 показан вертикально-сверлильный станок для выполнения сверлильных и сверлильно-резьбонарезных работ с диаметром сверления от 16 до 40 мм. Вертикальная сверлильная коробка скоростей 1 расположена на колонне 3, которая может иметь любое настроечное вертикальное перемещение. Несущая система наиболее распространенного типа станка состоит из основания-плиты 5 и колонны 3 (стойка). Основание служит опорой станка. Призматический вариант колонны рассматриваемого станка снабжен едиными направляющими, как для установочного перемещения сверлильной головки 1, так и для подъемного стола 4. В станках с призматической колонной на основании могут крепиться также неподвижные по высоте тумбы, крестовые, столы и иные вспомогательные устройства. Полости оснований используются как отстойники и резервуары для смазочно-охлаждающей жидкости. Номенклатура вертикально-сверлильных станков многообразна по назначению и применению в различных производственных. На рис. 4.29 показана часть станков. На рис. 4.29,в-г показаны варианты вертикально-сверлильного станка с круглой колонной. Поворотный (или неповоротный вокруг своей оси) стол имеет вертикальное установочное перемещение по колонне и поворачивается вокруг колонны на значительный угол. Станки используются в единичном и мелкосерийном производстве.
Шпиндельные узлы сверлильных станков испытывают значительные осевые нагрузки. С учетом этого в передней нижней опоре шпинделей применяются различные упорные и радиальные подшипники. Практически во всех станках используются выдвижные шпиндельные узлы пинольного типа, в которых поступательное движение рабочей подачи осуществляется перемещением гильзы шпинделя, связанной с механизмом подачи зубчато-реечной передачей. Для уравновешивания шпиндельных узлов часто предусматриваются притивовесы, которые размещены в колонне или по задней стенке колонны.
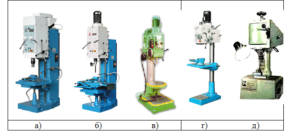
Рис. 4.29. Разновидности вертикально-сверлильных станков
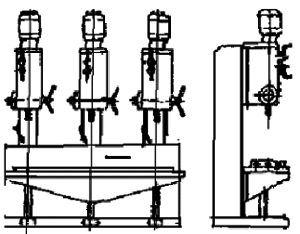
Рис. 4.30. Рядные сверлильные станки
Присоединительные места для инструмента концов шпинделей стандартизованы. В малых станках используются наружные конусы Морзе для крепления сверлильных или резьбовых патронов, в средних и крупных станках – внутренние конусы Морзе или конусы с конусностью 7:24.
Главный привод состоит из асинхронного электродвигателя и ременной передачи с многоручьевыми шкивами или вариатора. Используются также приводы с регулируемыми приводами. Основное исполнение главного привода ВВС с условным диаметром сверления 20 мм и более – с асинхронным электродвигателем и коробкой скоростей с вертикальными валами и перемещающимися зубчатыми блоками на 6-12 ступеней. Коэффициент ряда коробок скоростей обычно находится в пределах 1,26-1,6.Приводы подачи получают движение от шпиндельного или какого-либо другого вала главного привода и включают в себя коробку и механизм подачи линейного перемещения в конце звена.
В производственных условиях нередко используются рядные сверлильные или сверлильно-резьбонарезные станки с условным диаметром сверления 1-20 мм. (рис. 4.30). Группа одношпиндельных станков изготавливается с общим основанием и плитой (или подъемным столом) и состоит из двух- четырех станков. Используются в серийном производстве с закрепленной постоянной операцией на каждом станке, обычно в определенной последовательности технологии изготовления небольших по габаритам деталях.